“
背景简述
近年来,我国新能源汽车行业快速发展,消费者对新能源汽车的续航里程、驾驶安全性均提出了更高要求。通过对各类结构件的轻量化,能够提高新能源汽车续航里程,一般认为纯电动汽车重量每降低 10%,续航里程即可增加 6%。
动力电池作为新能源汽车的核心组件,重量占整车 20% 以上,其中,电池外壳约占电池系统总重量的 20%-30%。因此在保证电池系统功能安全和整车安全的前提下,电池壳的轻量化成为电池系统的主要改进目标之一。
电池外壳轻量化包括轻量化材料和对新制造工艺的应用,在满足安全性要求的前提下,主要以使用密度更低的材料来实现轻量化。
新能源动力电池外壳材料应用现状
目前,动力电池外壳材料以金属材料为主,主要为铝合金;同时非金属复合材料中的玻纤复合材料也已较多应用于动力电池上箱盖。碳纤维复合材料由于价格过高,仅有极少量应用于高端或豪华车型。
工程塑料复合材料目前尚未完全满足动力电池外壳对材料安全性的要求,尤其是在阻燃性和强度方面,因此仍处于验证使用阶段,未实现大规模商业应用。
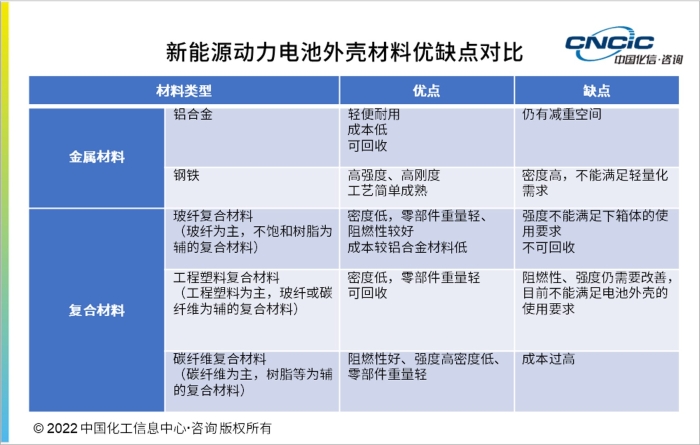
复合材料作为新兴新能源动力电池外壳材料,目前市面上共有四种生产工艺,分别为: SMC(片状模压)、LFT-D(长纤维增强热塑性塑料直接成型)、RTM(树脂传递模型或树脂压铸成型)、PCM(预浸料模压)。应用较广的玻纤复合材料,业内多简称为 SMC 复合材料。
复合材料在动力电池上的应用
由于不同类型新能源汽车在动力电池包安装位置、安全性要求等方面都有所不同,目前仅玻纤复合材料在中小型新能源汽车电池的电池上箱盖有较大规模使用。
碳纤维复合材料虽然上箱盖、下箱体均可使用,但限于生产工艺复杂、成本较高,仅在豪华车型上有少量使用。
工程塑料复合材料无法满足安全性要求,没有得到商业应用。
1
中小型新能源汽车:
上箱盖
中小型汽车电池的上箱盖不需要承重,因此该部件对材料的强度要求相对较低。玻纤复合材料凭借易加工以及较好的防火性能,在该领域的应用比重逐渐增加。
工程塑料复合材料的密度虽然比玻纤复合材料低,理论上能够进一步实现轻量化。但由于该类材料的阻燃性、强度有待改善,目前处于验证使用阶段。
业内已经开始尝试开发各类工程塑料复合材料,例如PPO+玻纤、PPS+玻纤、PC+玻纤等,力图将工程塑料应用于该领域,从而进一步加快电池包外壳轻量化。
下箱体
该部件要求承重,因此对材料强度要求较高。金属材料在该部件的应用暂时无法被其他材料大规模替代。
玻纤复合材料在强度上无法达到要求;虽然碳纤维复合材料在阻燃性和强度上均能过关,但制造成本过高;工程塑料复合材料在阻燃性和强度上均不能满足。
业内现已较多采用复合材料用于上箱盖,铝合金材料用于下箱体的方式进行电池外壳轻量化。以比亚迪为例,其采取了“上盖复合材料和下箱体铝材”的工艺以降低电池包壳体重量,使秦 Pro EV500 相比上一代车型,电池包减重 157kg。
2
大型新能源汽车:
该类汽车中尤其是新能源公交车因乘客多,十分看重整车安全性。当前主流的复合材料均不能满足其对强度及阻燃性的要求,未大批量商业化。而新能源卡车对轻量化不敏感,电池包外壳仍全部使用金属材料。
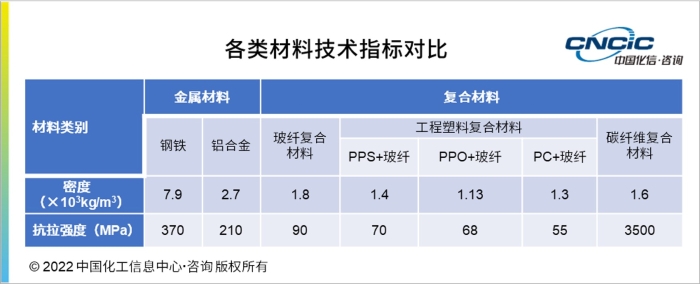
3
新能源动力电池外壳相关国家标准:
对动力电池外壳的技术要求被整合在《电动汽车用动力蓄电池安全要求》(简称“要求”)(GB 38031-2020)的相关规定中。《要求》提到的电池测试主要为了评估电池组在各种不利条件下的连接可靠性和结构完整性,要求试验后电池外壳无破裂、起火、爆炸、绝缘电阻过低的情况发生。
在挑选动力电池外壳材料时,动力电池生产商应考虑电池外壳能否通过《要求》中提到的相关测试。
一些企业为保证产品性能,企业标准往往会高于以上提及的国家标准。电池包生产商在选择新材料时,会要求其外壳生产商制造样品并对其进行测试,以确保材料的可靠性。有意向进入到该行业的材料供应商可考虑与电池外壳生产商联系,使用模具制备样品并进行安全性测试。
化信观点
动力电池外壳因需保护电池内部组件,所使用的材料必须具备优异的安全性能,尤其是较高强度和较好的阻燃性。
复合材料因密度更低的优势,开始替代金属材料在动力电池外壳上的应用,但现阶段由于安全性及成本问题,使用范围比较局限。仅有玻纤复合材料在中小型新能源汽车的电池上箱盖上得到大规模应用。
工程塑料复合材料作为密度更低,且可回收的材料,相关工程塑料公司如果希望进入该领域,需要进一步提高复合材料的强度、阻燃性等安全性能,为该类材料的大规模应用创造条件。